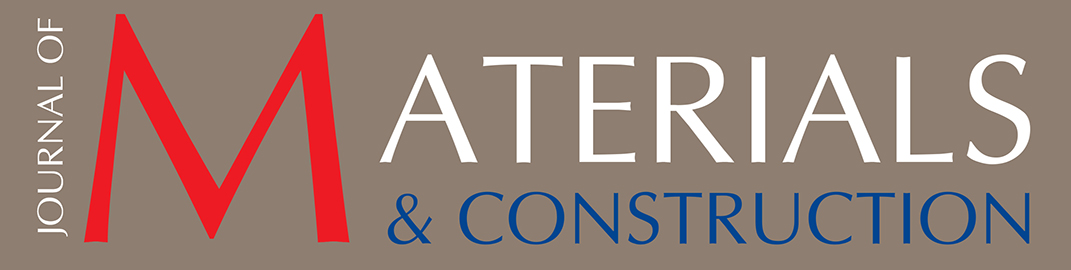
ISSN: 2734-9438
Website: www.jomc.vn
Bloating of fly ash-based lightweight aggregates
Abstract
The present work characterized two types of fly ash, one from pulverized coal combustion and the other from fluidized bed combustion. The effects of fly ash origins, raw mix proportions, and sintering temperatures on the bloating of lightweight aggregates were studied. The raw mixtures were calculated based on Riley's SiO2 – Al2O3 – fluxing composition diagram. The exothermic combustion reaction of a large amount of unburnt coal causes overheating, which results in boiling and abnormal bloating behavior. Besides, raw mixture compositions outside Riley's composition margin perform efficient bloating with most pore sizes from 0.5 to 1 mm. Hence, besides the fluxing content, one should consider the amount of unburnt coal in the fly ash in synthesizing lightweight aggregates.
References
- . H. Zhao, W. Sun, X. Wu, and B. Gao, "The properties of the self-compacting concrete with fly ash and ground granulated blast furnace slag mineral admixtures," Journal of Cleaner Production, vol. 95, pp. 66-74, 2015, doi: https://doi.org/10.1016/j.jclepro.2015.02.050.
- . T. Çiçek and Y. Çinçin, "Use of fly ash in production of light-weight building bricks," Construction and Building Materials, vol. 94, pp. 521-527, 2015, doi: https://doi.org/10.1016/j.conbuildmat.2015.07.029.
- . P. Topark-Ngarm, P. Chindaprasirt, and V. Sata, "Setting time, strength, and bond of high-calcium fly ash geopolymer concrete," Journal of materials in civil engineering, vol. 27, no. 7, p. 04014198, 2015, doi: https://doi.org/10.1061/(ASCE)MT.1943-5533.0001157.
- . E. Brännvall and J. Kumpiene, "Fly ash in landfill top covers–a review," Environmental Science: Processes & Impacts, vol. 18, no. 1, pp. 11-21, 2016, doi: https://doi.org/10.1039/C5EM00419E.
- . Y. Luo, S. Zheng, S. Ma, C. Liu, and X. Wang, "Ceramic tiles derived from coal fly ash: Preparation and mechanical characterization," Ceramics international, vol. 43, no. 15, pp. 11953-11966, 2017, doi: https://doi.org/10.1016/j.ceramint.2017.06.045.
- . L. Barbieri, I. Lancellotti, T. Manfredini, I. Queralt, J. Rincon, and M. Romero, "Design, obtainment and properties of glasses and glass–ceramics from coal fly ash," Fuel, vol. 78, no. 2, pp. 271-276, 1999, doi: https://doi.org/10.1016/S0016-2361(98)00134-3.
- . Y.-L. Wei, S.-H. Cheng, W.-J. Chen, Y.-H. Lu, K. Chen, and P.-C. Wu, "Influence of various sodium salt species on formation mechanism of lightweight aggregates made from coal fly ash-based material," Construction and Building Materials, vol. 239, p. 117890, 2020, doi: https://doi.org/10.1016/j.conbuildmat.2019.117890.
- . C. M. Riley, "Relation of chemical properties to the bloating of clays," Journal of the American ceramic society, vol. 34, no. 4, pp. 121-128, 1951, doi: https://doi.org/10.1111/j.1151-2916.1951.tb11619.x.
- . N. U. Kockal and T. Ozturan, "Optimization of properties of fly ash aggregates for high-strength lightweight concrete production," Materials & Design, vol. 32, no. 6, pp. 3586-3593, 2011, doi: https://doi.org/10.1016/j.matdes.2011.02.028.
- . K. Ramamurthy and K. Harikrishnan, "Influence of binders on properties of sintered fly ash aggregate," Cement and Concrete Composites, vol. 28, no. 1, pp. 33-38, 2006, doi: https://doi.org/10.1016/j.cemconcomp.2005.06.005.
- . T. Y. Lo, H. Cui, S. A. Memon, and T. Noguchi, "Manufacturing of sintered lightweight aggregate using high-carbon fly ash and its effect on the mechanical properties and microstructure of concrete," Journal of Cleaner Production, vol. 112, pp. 753-762, 2016, doi: https://doi.org/10.1016/j.jclepro.2015.07.001.
- . B. González-Corrochano, J. Alonso-Azcárate, and M. Rodas, "Effect of prefiring and firing dwell times on the properties of artificial lightweight aggregates," Construction and Building Materials, vol. 53, pp. 91-101, 2014, doi: https://doi.org/10.1016/j.conbuildmat.2013.11.099.
- . K. Mills, "How mold fluxes work," in Treatise on process metallurgy: Elsevier, 2014, pp. 435-475.