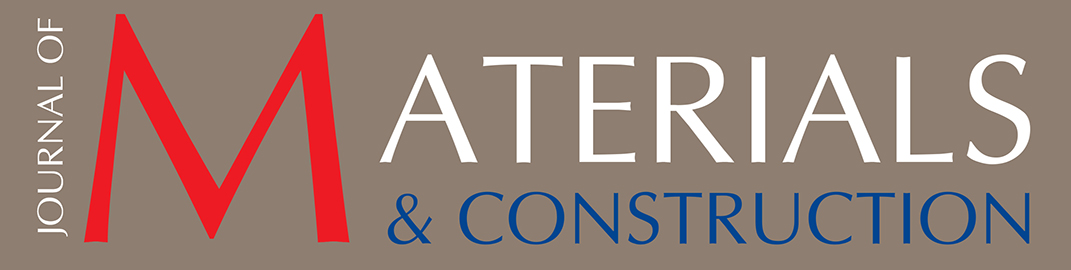
ISSN: 2734-9438
Website: www.jomc.vn
Chemical ddmixtures used in 3D printing of building materials
Abstract
Chemical admixtures present the key to successful 3D printing technologies. Moreover, many similarities between admixtures for dry-mix mortar and 3D printed mortar exist. This paper highlights current technologies and provides an outlook into which technologies might be required in the future. Generally, the kind of admixtures differ, depending on the type of 3D printing applied: extrusion, shot-crete or printing in particle bed. As of today, about 90% of actual work uses extrusion printing. In extrusion, immediate stiffening of the mortar is required once it leaves the nozzle. To achieve such sudden structuration, liquid alumina cement or crosslinking polymer systems are applied. Moreover, in order to avoid the sag of printed mortar layers, thixotropic agents based on nanoclays including attapulgite or meta muscovite are admixed. Additionally, adhesive polymers based on synthetic latex copolymers facilitate sufficient cohesion between individual printed layers and provide the necessary form stability of the structure. Early strength development can be achieved by nucleation enhancing admixtures ("seeding materials") such as those based on C-S-H-PCE nanocomposites. The working mechanisms of those admixtures and the benefits achieved from them will be disclosed in the presentation. A major hitherto unresolved problem is excessive shrinkage of 3D printed objects. It derives from chemical shrinkage (most mortars are very high in cement content) as well as physical/dry shrinkage (the absence of formwork to protect the surface from desiccation being the main reason here). So far, no technically satisfying and economical solution in actual application (i.e. not under controlled laboratory conditions) has been found, which requires future development work. In the future, more work will be devoted to print actual concrete which should be the ultimate goal, as it by far represents the most attractive application. However, to print concrete with steel embedded currently is considered to be unfeasible. To solve this problem, completely new approaches need to be taken to devise a realistic, field- suitable method.
References
- Leal, R., Barreiros, F. M., Alves, L., Romeiro, F., Vasco, J. C., Santos, M., Marto, C. (2017). Additive manufacturing tooling for the automotive industry. The International Journal of Advanced Manufacturing Technology, 92(5-8): 1671-1676.
- Wang, Y. C., Chen, T., Yeh, Y. L. (2019). Advanced 3D printing technologies for the aircraft industry: a fuzzy systematic approach for assessing the critical factors. The International Journal of Advanced Manufacturing Technology, 105(10): 4059-4069.
- MacDonald, E., Wicker, R. (2016). Multiprocess 3D printing for increasing component functionality. Science, 353(6307).
- Lee, S. (2016). Prospect for 3D printing technology in medical, dental, and pediatric dental field. Journal of The Korean Academy of Pediatric Dentistry, 43(1): 93-108.
- First RILEM International Conference on Concrete and Digital Fabrication – Digital Concrete 2018, Zürich, Switzerland
- Scaling Up 3D – the Interdisciplinary Symposium on Printable Mortars; 2019, drymix.info, Vienna, Austria
- Digital Concrete 2020 - 2nd RILEM International Conference on Concrete and Digital Fabrication, Eindhoven, Netherlands
- Buswell, R. A., De Silva, W. L., Jones, S. Z., Dirrenberger, J. (2018). 3D printing using concrete extrusion: A roadmap for research. Cement and Concrete Research, 112: 37-49.
- DIN EN 1015-3: 2007-05. Methods of test for mortar for masonry - Part 1: Determination of particle size distribution (by sieve analysis); German version EN 1015-1:1998+A1:2006.
- DIN EN 12004: 2014-02. Adhesives for tiles - Requirements, evaluation of conformity, classification and designation; German version EN 12004:2007+A1:2012
- DIN EN 196-3: 2009-02. Methods of testing cement - Part 3: Determination of setting times and soundness; German version EN 196-3:2005+A1:2008.
- DIN EN 196-1: 2016-11. Methods of testing cement - Part 1: Determination of strength; German version EN 196-1: 2016.
- API RP 13B-1. (2009). Recommended Practice for Field Testing Water-based Drilling Fluids. 4th Edition: American Petroleum Institute, Washington DC.
- Plank, J., Sakai, E., Miao, C. W., Yu, C., Hong, J. X. (2015). Chemical admixtures—Chemistry, applications and their impact on concrete microstructure and durability. Cement and Concrete Research, 78: 81-99.
- Imerys, product information - Exalt®, Vaulx-Milieu, France.
- Pickelmann, J., Plank, J. (2012). A mechanistic study explaining the synergistic viscosity increase obtained from polyethylene oxide (PEO) and β-naphthalene sulfonate (BNS) in shotcrete. Cement and Concrete Research, 42: 1409-1416.
- Ravi, K., Krishnakumar, B., Swaminathan, M. (2012). An efficient protocol for the green and solvent-free synthesis of azine derivatives at room temperature using BiCl3-loaded montmorillonite K10 as a new recyclable heterogeneous catalyst. International Scholarly Research Notices, 2012.
- Li, Q., Ju, L., Lu, M., Zhang, Y., Xu, S., Li, Z. (2018). Significant improvement of styrene oxidation over mononuclear/binuclear carboxyl metal phthalocyanine-attapulgite composites. Fullerenes, Nanotubes and Carbon Nanostructures, 26(12): 791-798.
- Plank J. (2019). "Bauchemie” in: Zilch K., Diederichs C. J., Beckmann K. J., Gertz C., Malkwitz A., Moormann C., Urban W., Valentin F. (Eds), “Handbuch für Bauingenieure”, Springer Verlag, p. 1 – 57.
- Suiker, A. S., Wolfs, R. J., Lucas, S. M., Salet, T. A. (2020). Elastic buckling and plastic collapse during 3D concrete printing. Cement and Concrete Research, 135: 106016.
- Prudencio Jr, L. R. (1998). Accelerating admixtures for shotcrete. Cement and Concrete Composites, 20(2-3): 213-219.
- Kanchanason, V., Plank, J. (2018). Effectiveness of a calcium silicate hydrate–Polycarboxylate ether (CSH–PCE) nanocomposite on early strength development of fly ash cement. Construction and Building Materials, 169: 20-27.
- Dedehayir, O., Steinert, M. (2016). The hype cycle model: A review and future directions. Technological Forecasting and Social Change, 108: 28-41.